Liquid Lithium Heat Flux Transport Inside a Tokamak Fusion Reactor
- Researcher: Oliver Bond
- Academic Supervisors: Peter Howell, John Ockendon
- Industrial Supervisor: Peter Buxton
Background
Tokamak Energy is a nuclear fusion company based in Milton Park, Didcot. They have built a device called a tokamak (derived from the Russian word, meaning “toroidal chamber with magnetic field”) with the aim of replicating the physical conditions required for nuclear fusion. This device is called the ST40, which can be considered a “prototype” for an actual fusion reactor. ST40 has achieved temperatures of 15 million degrees Celsius (with 100 million being the ultimate goal) yet is contained within a torus of only 40 cm radius and only runs for a quarter of a second! Figure 1 shows the key features of the ST40; in particular, the plasma (a "sea" of delocalised ions) which is confined by magnetic fields generated by strong electrical currents in large coils.
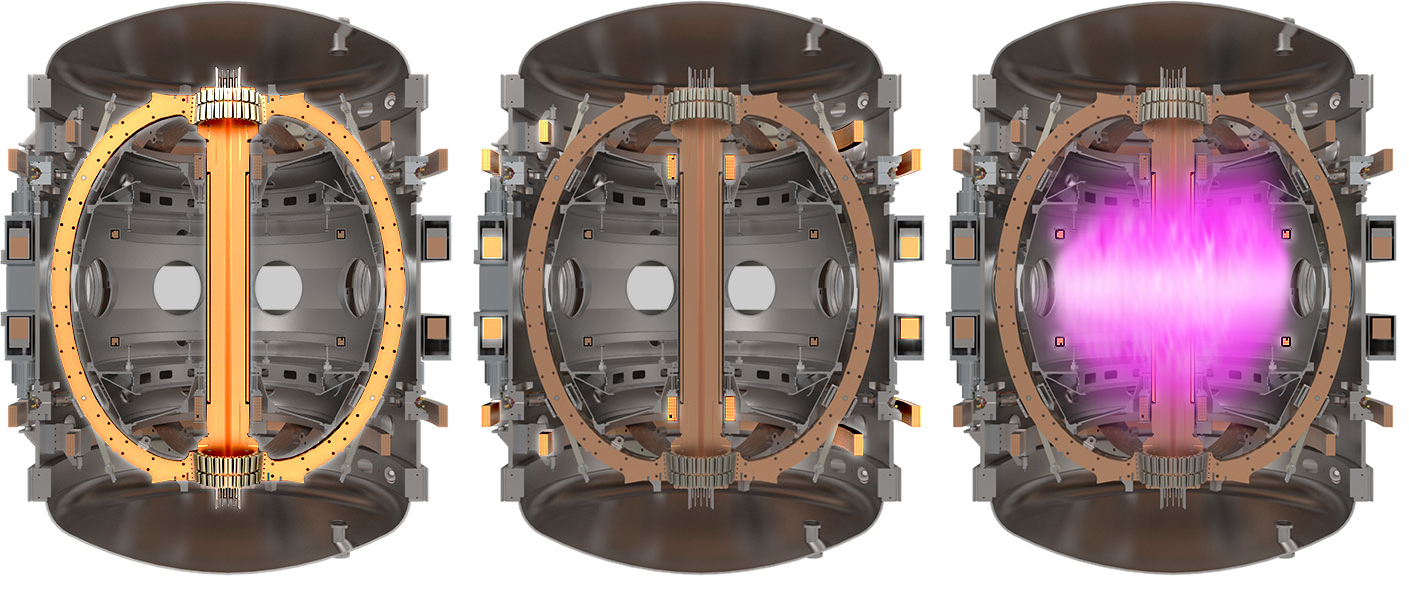
Figure 1: Cross-sections of the ST40 device built by Tokamak Energy, with different parts highlighted: poloidal coils (left), toroidal coils (centre) and the plasma confinement region (right).
At the top and bottom of ST40 is a component called the divertor. This is an axisymmetric substrate, resembling the slanted surface of a truncated cone. It is where exhaust heat energy and waste particle matter is deposited from the plasma. The divertor needs to repeatedly withstand a heat flux larger than that of a space shuttle upon re-entry (about 10 MW/m²). Traditional solid divertors become very hot and can suffer from erosion, and we want to avoid replacing them every few months or years. Thankfully, strategies for cooling the divertor have been explored; for example, by using a thin layer of liquid lithium to carry the heat flux away from the plasma. However, liquid lithium divertors present their own challenges, such as dryout, where the underlying solid material is eroded by the plasma where liquid lithium is absent.
One solution that has emerged in the past is a concept known as Liquid Metal-Infused Trenches (LiMIT) which was created at the University of Illinois at Urbana-Champaign (UIUC). This consists of a series of parallel trenches down which liquid lithium flows, thus forming a sort of "heat flux conveyor belt". This concept exploits a quantum phenomenon known as the thermoelectric (or Seebeck) effect, where passing a temperature gradient along a interface between two electrical conductors results in an electrical current along that interface. When combined with a magnetic field applied across the trench, this results in a Lorenz force which drives the flow down the trench. Although the classical LiMIT device consists of rectangular trenches, we are interested in investigating whether there is a trench shape which maximises the average fluid velocity down the trench, which Tokamak Energy believe to be a good "proxy" for the amount of heat flux transported. We are therefore interested in mathematically modelling the behaviour of the liquid lithium inside a trench of arbitrary cross-sectional shape. An illustration of a single trench is shown in Figure 2.
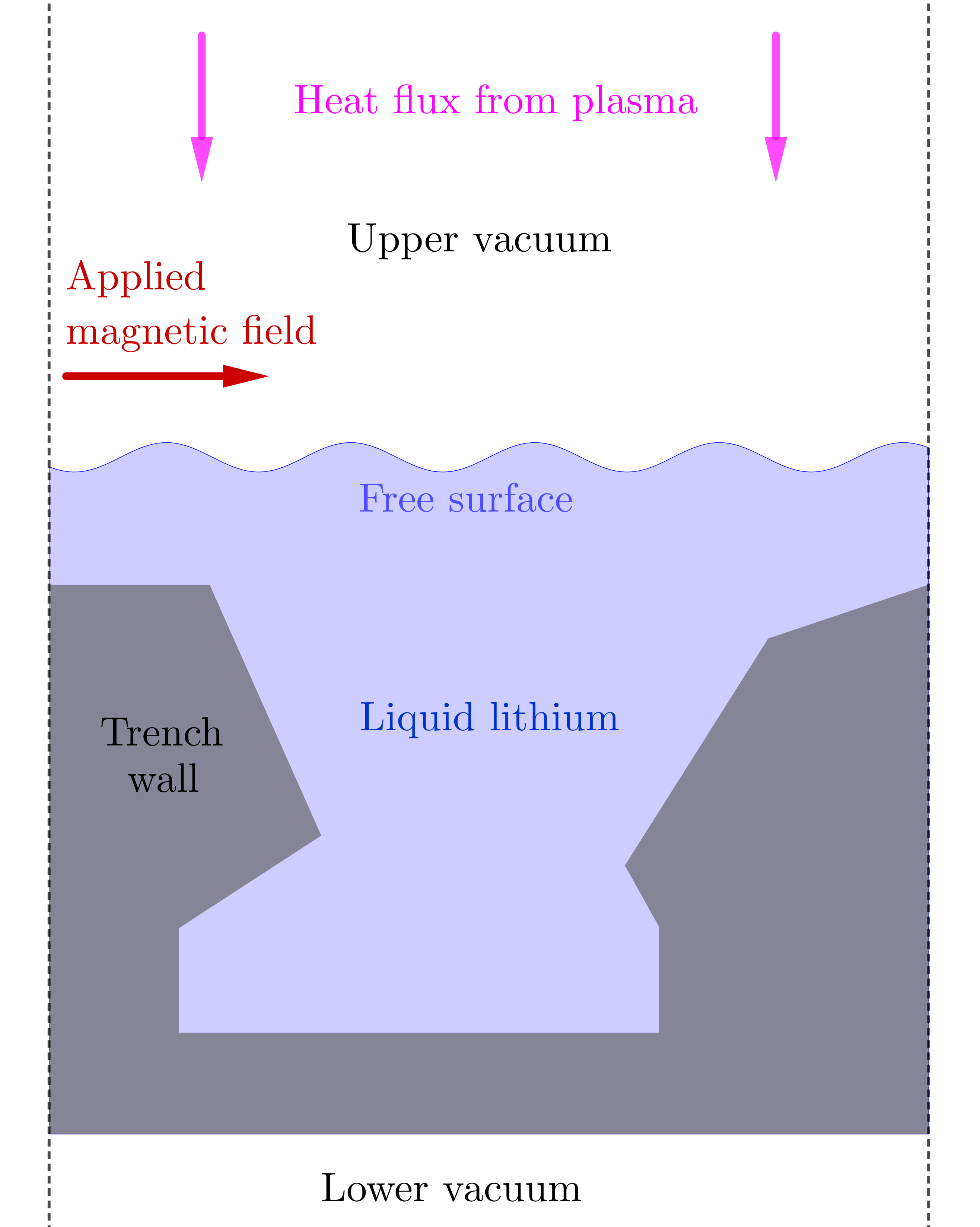
Figure 2: A schematic showing the physical setup of a single LiMIT-style trench.
Progress
In our modelling work, we have combined Maxwell's equations of electromagnetism with the Navier-Stokes equations of fluid dynamics, thus working with the equations of magnetohydrodynamics (MHD). Incorporating the heat equation and the Seebeck effect turns this into a model involving thermoelectric magnetohydrodynamics (TEMHD). Using TEMHD principles, we have derived a mathematical model which governs the relevant physical quantities (including the fluid velocity $u$, magnetic field $B$ and temperature $T$) in unidirectional flow down the trench. At leading order, we showed that the free surface must be flat, that the pressure is constant, and that the temperature decouples from the governing equations relating $u$ and $B$. We also find that the fluid flow is driven entirely by the temperature gradient normal to the free surface.
The problem also involves a small parameter $\epsilon$, equal to the reciprocal of the Hartmann number ${\rm Ha}$, which measures the ratio of electromagnetic to viscous terms in the Navier-Stokes equation and is typically large ($~10^2$) in fusion applications. The appearance of $\epsilon$ in the problem makes the problem that we derived amenable to methods from an area of applied mathematics known as singular perturbation methods. Furthermore, the problem we derived draws many parallels to classical MHD duct flow problems, such as that of Shercliff in 1953. To better understand the tools required to be able to tackle the LiMIT-type problem, we apply asymptotic and numerical methods to the Shercliff problem, which forgoes much of the physics (e.g. temperature, free surface, conducting walls) yet serves as an important conceptual foundation.
The Shercliff 1953 problem considers unidirectional MHD flow of liquid metal down a rectangular duct with thin, electrically insulating walls, with a constant applied magnetic field in the positive horizontal direction. Shercliff found an exact solution to the problem, but found that the solutions are only well-behaved when ${\rm Ha}$ is large. We studied this classical problem, but this time introducing the aspect ratio $\ell=b/a$ as a parameter in the problem. Using asymptotic and numerical analysis, we obtained velocity profiles which exhibit so-called Hartmann layers and thicker side layers. These are thin, confined regions near the walls of the duct in which the viscosity of the walls suddenly becomes important and acts to slow the fluid down to a standstill close to the walls. Both these layers are relatively thin and become even thinner as ${\rm Ha}$ increases, as Figure 3 illustrates.
However, rather than simply solving for the velocity and magnetic field, we wish to determine whether there is an aspect ratio $\ell$ for which the mean flow rate of fluid down the duct is maximised, if the area of the duct is constant. We successfully found a relationship between $\ell$ and $\epsilon$ in which this does happen, and confirmed this using both asymptotic and numerical analysis. These findings are significant, because the role of the aspect ratio has been seldom considered in classical MHD duct flow literature as a varying parameter.
Future Work
There are many interesting avenues that can arise as a result of this work. The first step is to adapt the asymptotic and numerical approaches to solve the unidirectional trench model that we have derived, and this is something we are currently working towards by gradually implementing more general physical effects in the Shercliff model that we have already solved.
There is freedom to optimise the geometry of the trench wall, for example, to maximise the flow rate of the liquid down the trench or to minimise the surface temperature of the lithium. Surface temperature needs to be controlled carefully in order to minimise the extent to which undesirable evaporation happens, as lithium impurities can cause the plasma performance to deteriorate. Thinking about the problem in this way could lead to it being recast as an optimisation problem using applied mathematical techniques collectively known as the calculus of variations. Simple shapes which generalise the simple rectangular design proposed at UIUC can be tested numerically and experimentally, as they have virtually no constraints on the shapes they can machine.
Recent communications with Tokamak Energy and UIUC have highlighted several more areas of interest. In particular, they have extended upon LiMIT by introducing gaps which allow liquid lithium to flow between neighbouring trenches; a phenomenon that UIUC call "cross-talk". This in effect results in a divertor plate which appears to have many "posts" in it, which in their current state resemble cuboids whose dimensions are several millimetres. Tokamak Energy and UIUC are interested in optimising the post geometry. The justification for this design choice is that it seems blockages inside a trench can only be resolved by driving the flow further through thermoelectric currents, whilst flow between channels allows the liquid in neighbouring trenches to be replenished more easily. This is particularly necessary if the distribution of liquid lithium from the inlet is uneven.
The mathematical work carried out here in Oxford serves as a way rigorously validate experimental and numerical observations by UIUC and Tokamak Energy.