Modelling the carding of recycled carbon fibre
- Researcher: Joe Roberts
- Academic Supervisors: Peter Howell, Hilary Ockendon
- Industrial Supervisor: Mathilde Poulet
Background
In recent years the demand for carbon fibre has increased, mainly due to its wide variety of potential industrial applications, including the use of carbon fibre-reinforced materials in the aerospace, automotive, and defence industries. Carbon fibre has a number of advantageous properties that make it highly versatile. For example, it has a very high tensile strength and low density. The current high demand, which is predicted to rise in the future, means that the amount of waste carbon fibre is increasing. ELG Carbon Fibre (ELGCF) recover carbon fibre waste from the aerospace industry and turn it into non-woven materials that can be used in other industries, such as the automotive industry.
ELGCF's processing of waste carbon fibre involves multiple stages. We examine the carding stage of this process, where the carbon fibres are passed through a carding machine, which turns the disordered web of fibres entering the machine into a homogeneous oriented web of aligned fibres that can then undergo cross-lapping and needling. Carding machines are widely used in the textile industry, and consist of a set of toothed cylinders of different sizes, moving at different velocities. In Figure 1, we see the three cylinders we focus on, the worker, stripper and main cylinder, and their relative directions and sizes. Our aim is to derive and validate a continuum model for the flow of material through the carding machine, which will then allow us to predict the control parameter values that will optimise the process.
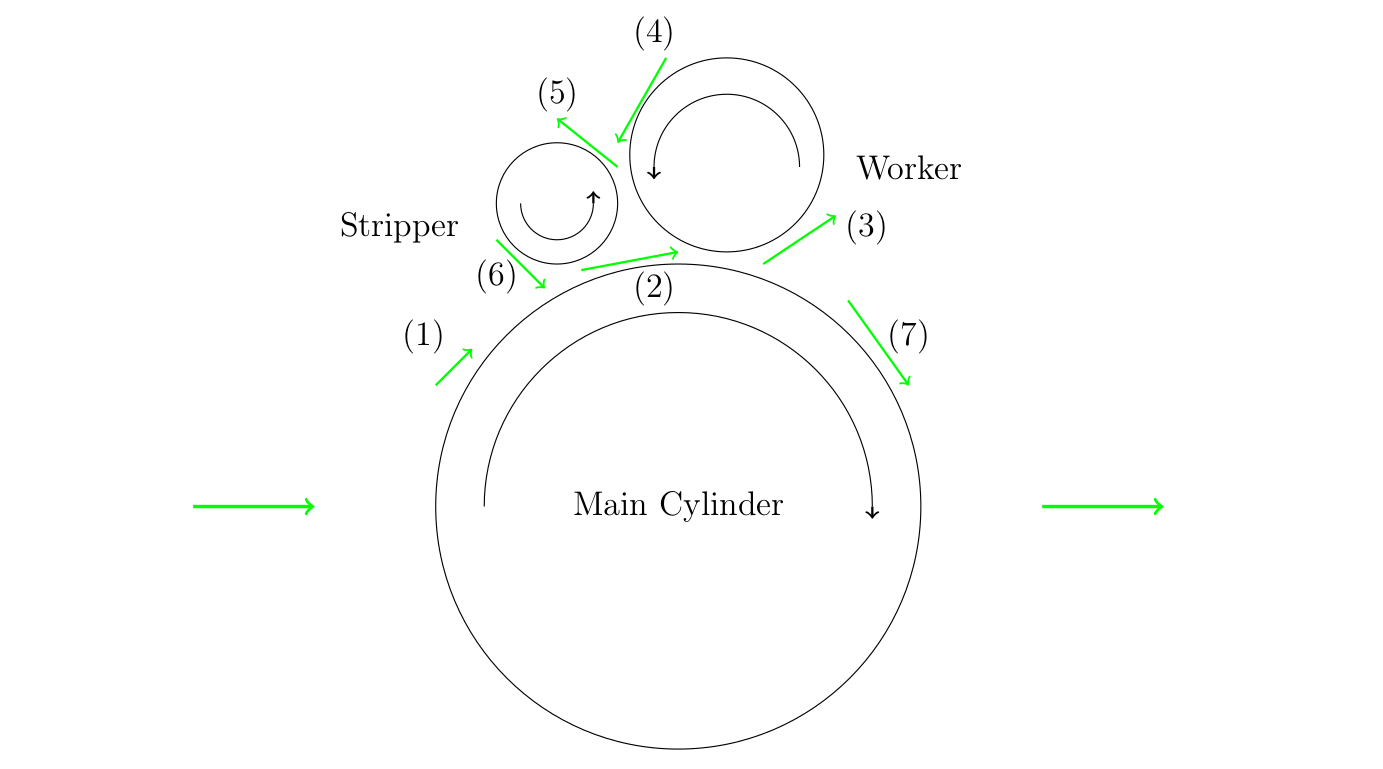
Figure 1: The path of a fibre (shown in green) through a section of the carding machine. The typical order is shown by numbers (1)-(7).
Progress
We have adjusted an existing model for carding in the textile industry to fit the properties of carbon fibre. We have derived a continuum model for the flow of fibres in a thin region, making use of the fact that the distance between the cylinders is much less than the radii of the cylinders. An example of one of these regions is shown in figure 2. The model consists of equations for conservation of mass, conservation of momentum, a kinematic condition, and a constitutive law for the order parameter. In this model, we assume that the fibres become more ordered as they are stretched. The order parameter is a measure of how aligned the carbon fibres are, being equal to 1 if the fibres are fully aligned, and 0 if they are randomly oriented. Using this model, we can view how the density and order of the fibres change through the different regions of the carding machine. The model also allows us to vary the velocities of the cylinders, and we find that a large velocity difference is optimal for maximum ordering.
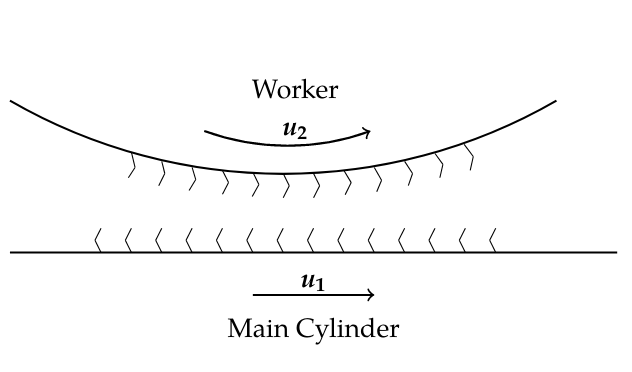
Figure 2: Picture showing the region between the worker and the main cylinder.
Further Work
We will adjust our model to include the effect of the hooks along the cylinders (shown in Figure 2) as well as the stretching of the fibres via the motion of the cylinders. Two ways in which we will approach this are, adjusting our existing model to include point forces, and looking at the forces on a fibre as it is being combed by a hook, thus changing the constitutive law for the order parameter. The aim of future work will be to derive models for all parts of the carding process, including cross-lapping and needling, and then develop a tool for optimising the product of the carding process.