Modelling chemical and transfer processes in a concept silicon reactor
- Researcher: Brady Metherall
- Academic Supervisors: Chris Breward, Colin Please, James Oliver
- Industrial Supervisors: Aasgeir Valderhaug, Ben Sloman
Background
Typically silicon is produced in an electrode-submerged furnace. A large current passes through the electrodes and through quartz and various forms of carbon: coal, charcoal, woodchips. The current heats and melts the raw materials, which allows chemical reactions to initiate. Carbon monoxide and carbon dioxide are by-products of these reactions that end up being emitted into the atmosphere. Elkem is researching alternate silicon processes to reduce carbon emissions.
One particular process involves coating a quartz particle with a thin layer of carbon by depositing renewable methane. These pellets can then be added to a concept furnace, at a much lower temperature than a standard furnace. Due to the nature of the pellets, and the reduced temperature, the set of chemical reactions that take place is different. The result is silicon carbide, which can then easily be processed into silicon.
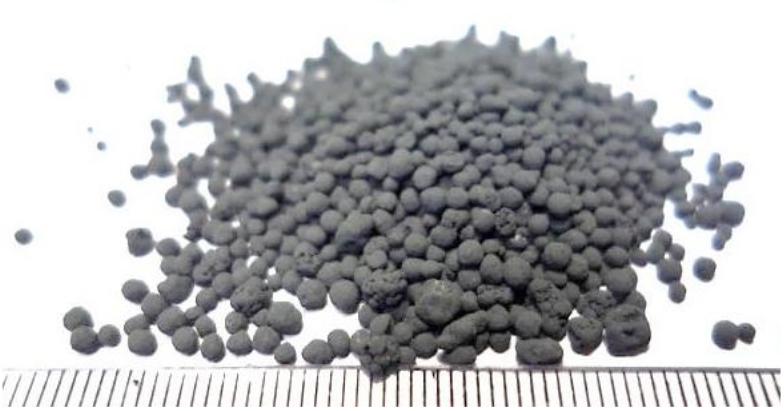
Figure 1: Quartz-carbon pellets.
Outcomes
We build a mathematical model to encapsulate the relevant chemical reactions, as well as the transport of the chemicals through the pellet. Currently, we are focusing on a micro-scale model for a single pellet. We have developed a model of coupled partial differential equations that capture the evolution of chemical concentrations, gas flow, the consumption of the quartz core, and the conversion of the carbon shell to silicon carbide. By assuming the dynamics in our single pellet are radially symmetric, we are able to reduce our model to one spatial dimension. We can make further simplifications by non-dimensionalising the model, and performing an asymptotic analysis. We are now using numerical simulations to explore the different parameter regimes. Varying properties of the pellet, such as the size of the pellet or the thickness of the carbon layer, changes the relative strength of the dynamics in the pellet.
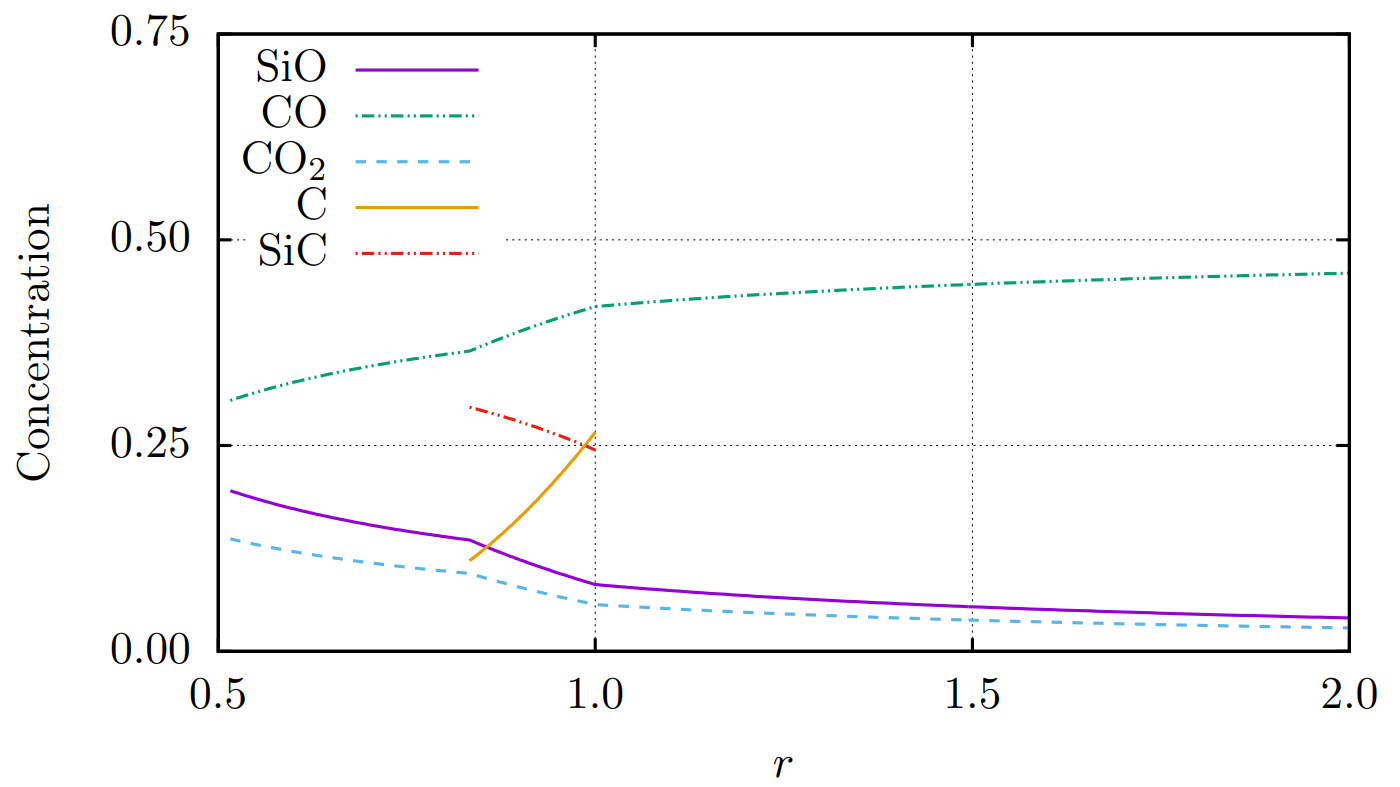
Figure 2: Concentration of gases and solids. The quartz is consumed by carbon monoxide, creating a void between the quartz and the carbon shell.
Future Work
Once we fully understand our single pellet micro-scale model, we can up-scale the model to the macro-scale to model an entire furnace. This would allow us to take into account the effect a pellet has on its neighbours, and optimise the design of the furnace to minimise carbon monoxide emissions or maximise silicon carbide production, for example.