Material flow in a silicon furnace
- Researcher: Matthew Shirley
- Academic Supervisors: Colin Please, Jim Oliver, Matthew Moore
- Industrial Supervisor: Aasgeir Valderhaug, Anne Gry Messenlien, Ben Sloman
Background
Silicon is a very common material used in everything from solar panels to cooking utensils, or smartphone processors to medical devices. However, despite being the second most abundant element in the Earth’s crust, it is never found in a pure form. Instead, quartz rock must be industrially processed in a submerged arc furnace to extract the silicon. In a submerged arc furnace (see figure 1) quartz and carbon are added at the top to form a mixture called the charge. The charge is then heated as it descends through the furnace creating silicon and several process gases via a series of chemical reactions. The quartz will also soften and melt causing a transition from a granular flow to a viscous one. Once the semi reacted charge nears the bottom of the furnace a solid crust region will form, creating a hollow crater below filled with gas. The position of the crater’s walls is known to have a major effect of the furnace's efficiency.
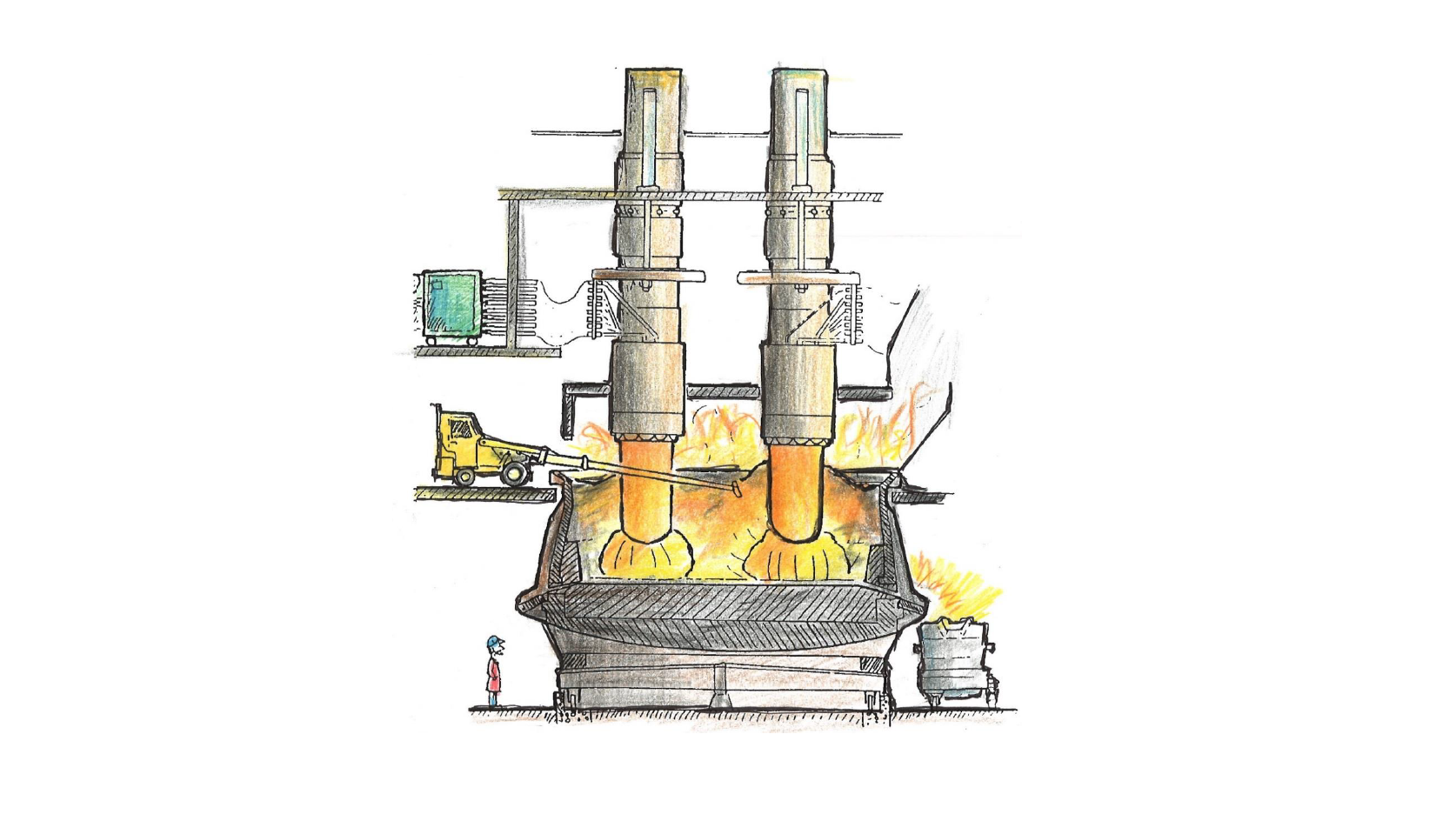
Figure 1: A sketch of a silicon furnace. Reproduced from The Si Process Drawings, by Thorsteinn Hannesson.
This research project will use a combination of analytical and numerical methods to model the strongly coupled behaviour of the charge material, process gases, and temperature in the furnace. We will seek to predict when and where clogging, channelling, and crater walls will form. Since quartz has a wide range of thermal and mechanical properties, depending on its source, we shall also study how the occurrence of the processes differs for different raw materials. This will help our partner company Elkem ASA to make better informed choices about how and which quartzes to use in their furnaces.
Progress
We have begun studying the flow of gas through channels in the charge material (see figure 2). When these channels become large enough, a furnace operator will stoke the furnace, remixing the charge and destroying these channels. We model the gas using the compressible Navier-Stokes equations. We prescribe the temperature on the wall to model the temperature of the charge material. Using this model, we can predict how much energy is transferred the from the gas to the charge. This is important as it will help us to understand whether the gas flow is the dominant factor in heating up the charge, or whether it is the chemical reactions or conduction through the solid charge. To investigate this further we are incorporating chemical reactions between the gas and charge material on the wall and are allowing this to evolve the shape of the channel.
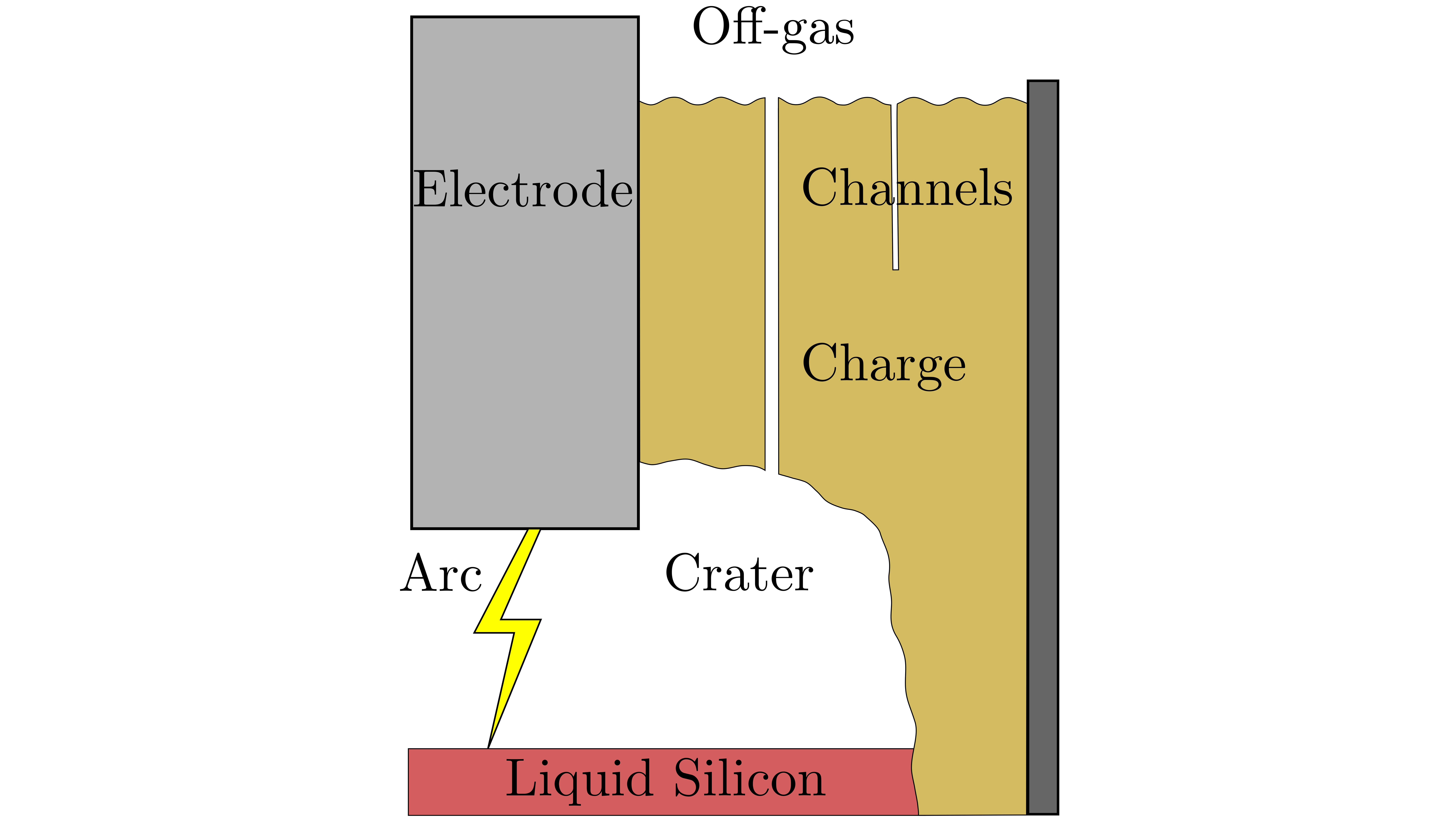
Figure 2: The different regions of the furnace.
Future Work
We shall couple our channel model to one for the flow of gas through a porous medium representing the charge. This will allow us to determine if a few small channels carry most of the process gas to the surface, or if the gas spreads out through the entire charge before reaching the surface.
In the longer term we shall consider modelling the flow of charge itself. This will initially be done by assuming we know the behaviour of the gas phase, mirroring our approach for the gas phase where we assumed the behaviour of the charge. Finally, we will try to join our two models to form a full model of the furnace.